|
POWDER SPHEROIDIZATION
Powder spheroidization is the transformation of either agglomerated powders produced by spray drying and sintering techniques, or angular powders produced by conventional crushing methods, into spherical powder.
Induction plasma technology is used to achieve this through in-flight heating and melting of feed material particles followed by cooling and solidification under controlled conditions.
The spherucal powders can cater to a range of applications such as
hard surfacing, cold spray, thermal spray, metal injection molding
and additive manufacturing.
The key advantages of powder spheroidization are as follows:
- Improves flowability
- Reduces internal porosity
- Higher packing density
- Less friable powder
- Increases purity
Example of the improvement in the quality of tungsten carbide
powder:
PROPERTIES |
BEFORE POWDER
SPHEROIDIZATION |
AFTER POWDER
SPHEROIDIZATION |
Photograph |
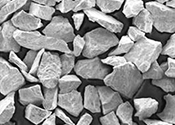 |
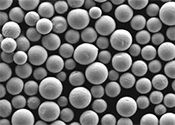 |
Particles |
WC (-100+400 Mesh/40-150um)
|
WC (-100+400 Mesh/40-150um) |
Tap Density |
8.1 g/cm3 |
10.2g/cm3 |
Hal Flow Test |
19sec/50g |
7sec/50g |
Aeromac Thermal provides a range of
Tekna powder spheroidization equipment using their unique
spheroidization process. We also offer a range of spherical powders manufactured by Tekna's
powder spheroidization technology.
Tekna is a world leader in induction plasma
technology, ensuring the highest level of quality and innovative
equipment and powders.

POWDER SPHEROIDIZATION SYSTEMS
EQUIPMENT |
BRIEF |
SPHEROIDIZABLE
MATERIALS |
TekSphero-15
|
- PQ-35 Tekna’s Induction plasma torch
- Manual operation
- Very flexible for batch process
- Reactor enclosed within laminar flow hood
- Foot print LxWxh (m): 2.5 x 0.9 x 2.0
- Min. floor space LxWxh (m): 3.7 x 2.0 x 2.4
|
The
technology can spheroidize the following (not limited to)
- Ceramics Oxide
- Ceramics Non-oxide
- Pure Metals
- Alloys
- Etc
Capacity of plasma treatment
- Purity Enhancement Factor: Up to 10x
- Densification Factor: Up to 3x
- Spheroidization: Up to 100%
- Melting Point: No limit
- Raw Material Types: Crushed, Sponge, Fibres,
Atomized Solution
|
TekSphero-40
|
- PN-35 Tekna’s Induction plasma torch
- Advanced touch screen interface
- Data logging
- Manual control
- Foot print LxWxh (m): 4.6 x 3.8 x 2.9
- Min. floor space LxWxh (m): 8.2 x 7.5 x 3.6
|
TekSphero-80 |
- PN-50 Tekna’s Induction plasma torch
- Advanced touch screen interface
- Data logging
- Automated control
- Foot print LxWxh (m): 5.4 x 3.2 x 2.9
- Min. floor space LxWxh (m): 9.0 x 7.5 x 3.6
|
TekSphero-200 |
- PN-70 Tekna’s Induction plasma torch
- Advanced touch screen interface
- Data logging
- Automated control
- Gas recycling
- Foot print LxWxh (m): 8.7 x 6.5 x 6.8
- Min. floor space LxWxh (m): 12.3 x 10.2 x 8.2
|
Custom Systems |
We can work
with you to help address specific requirements for
customized equipment and turn key processes. |
SPHERICAL POWDERS
SPHERICAL
POWDER |
BRIEF |
Cast Tungsten
Carbide (SCWC) |
These powders are manufactured by Tekna's state-of-the-art
powder spheroidization equipment. They are well-known for their superior quality and uniformity, and offer higher density, higher purity and better flow than standard powders. They are an excellent choice of precursor for applications requiring high quality materials. |
Tungsten |
Titatium
Carbide (TiC) |
Tantalum |
Molybdenum |
Silicon Dioxide |
Silicon |
Commercially
Pure Titanium (CPTi) |
Titanium
Aluminium Vanadium |
Custom
Spherical Powders |
We can work with you to help address specific requirements for customized materials and specifications (e.g. Alumina, Boron Carbide, Copper, Niobium Carbide, Vanadium Carbide etc) |
Contact us
for technical data sheets, more information or any other enquiries.
|
|